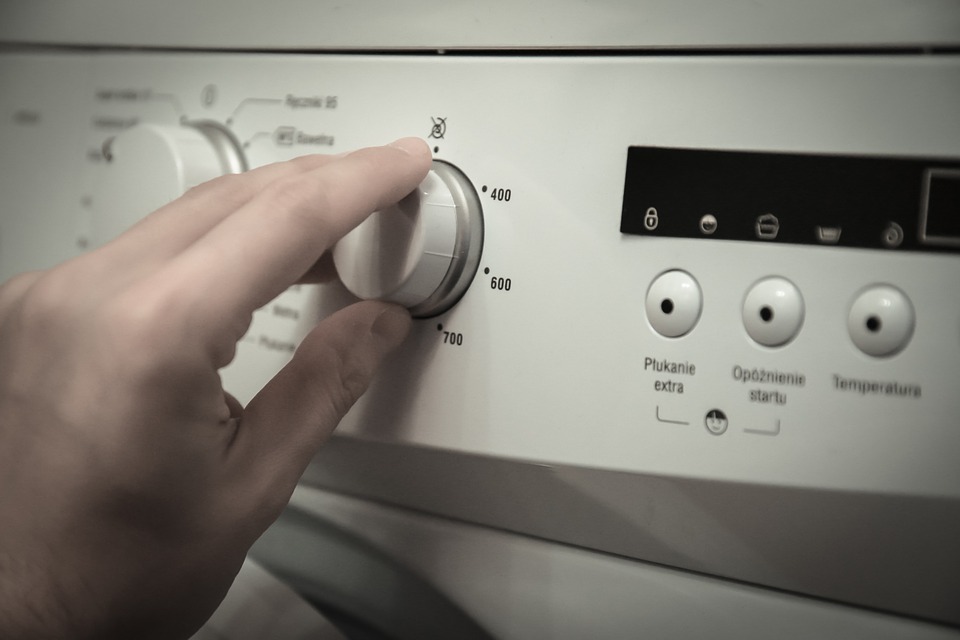
Na co zwrócić uwagę, kupując pralkę?
28 grudnia 2016Posadzka poliuretanowa czy epoksydowa?
22 lutego 2017Recykling katalizatorów: cele i metody
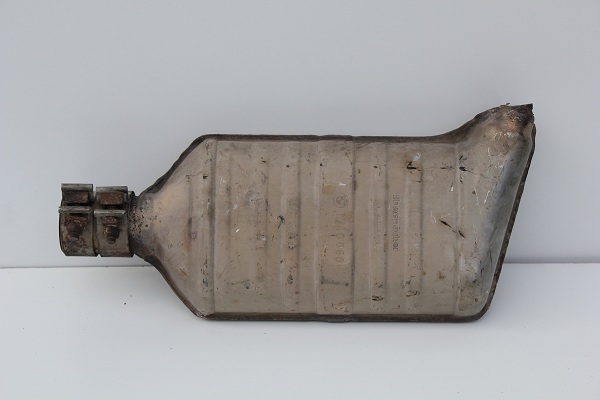
Zagadnienia ekologiczne mają współcześnie ogromny wpływ na szereg gałęzi nauki i przemysłu. Także w przypadku przemysłu motoryzacyjnego, stale zaostrzane normy emisji szkodliwych substancji do atmosfery, wymusiły na producentach powszechne stosowanie instalacji ograniczających zanieczyszczenie środowiska naturalnego.
Działanie reaktorów katalitycznych, popularnie zwanych katalizatorami, polega na wykorzystaniu aktywnych chemicznie metali (głównie platynowców), które wykazują zdolność do przekształcania substancji szkodliwych, w tym tlenku węgla (II), tlenków azotu i węglowodorów, na mniej niebezpieczne: wodę, azot i dwutlenek węgla.
Budowa katalizatora, czyli poszukiwanie skarbów
Typowy katalizator to konstrukcja zbudowana na bazie jednego lub dwóch bloków ceramicznych lub też blachy, które zlokalizowane są w obudowach układu wydechowego. Elementy te pokryte są specjalną porowatą strukturą – gęstą siatką kwadratowych otworów, która do złudzenia przypomina plaster miodu. Powierzchnia ta pokryta jest bardzo cienką warstwą metali szlachetnych (platyny, palladu oraz rodu), które jako aktywatory procesów chemicznych, skutecznie neutralizują szkodliwe związki, zamieniając je na inne.
To właśnie platynowce sprawiają, że recykling katalizatorów stał się ogromnym rynkiem, na którym istotną rolę odgrywają także polskie firmy, jak na przykład renomowana spółka o ponad 20 letnim stażu na rynku.
Metody przerobu katalizatorów
Przerób katalizatorów w celu odzyskania zawartych w nich metali szlachetnych stał się procesem przemysłowym. Aby osiągnąć jak największą wydajność, wykorzystuje się tutaj specjalistyczne technologie:
Wśród metod hydrometalurgicznych można wymienić:
- chlorowanie,
- rozdzielanie,
- ekstrakcję cyjankami,
- ekstrakcję wodą królewską.
Wśród metod pirometalurgicznych można wymienić:
- metodę stapiania,
- metodę ROSETM,
- obróbkę termiczną (Metal Vapour Treatment).
Jak przebiega proces recyklingu?
Proces odzyskiwania metali szlachetnych z katalizatorów można podzielić na główne etapy:
- pierwszym krokiem jest zebranie i wstępna obróbka pozyskanego materiału,
- następnie przeprowadza się szczegółową analizę próbek pobranych ze wsadu,
- uzyskane platynowce zostają rozpuszczone w procesach ekstrakcji, strącania lub destylacji,
- platyna, pallad oraz rod odzyskiwane są w procesie redukcji, ekstrakcji albo procesach elektrolitycznych,
- rafinacja platynowców wymaga zastosowania technologii hydrometalurgicznych.